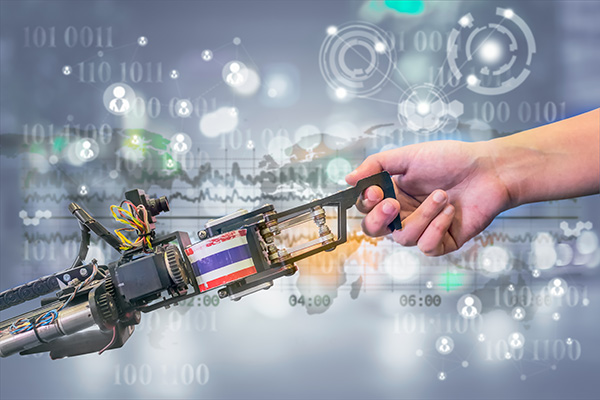
“ประเด็นสำคุณจากการบรรยายในหัวข้อ Industry Transformation Practice and Case โดย ศักดิ์พัฒน์ วิทยศักดิ์ กรรมการผู้จัดการ บริษัท โซลดิฟ จำกัด ผู้เชี่ยวชาญอุตสาหกรรม 4.0 และระบบ IoT ที่ทำให้ภาพของการเปลี่ยนผ่านอุตสาหกรรมด้วยการวิเคราะห์ข้อมูลและเข้าใจผู้บริโภคในเชิงลึก
คณะเทคโนโลยีสารสนเทศ มหาวิทยาลัยศรีปทุม จัดบรรยายพิเศษโครงการบัณฑิตพันธุ์ใหม่ ด้าน IT (NON DEGREE), RE SKILL- UP SKILL รุ่นที่ 2 ปีการศึกษา 2563 สำหรับหลักสูตร การเปลี่ยนผ่านอุตสาหกรรมด้วยการวิเคราะห์ข้อมูลและเข้าใจผู้บริโภคในเชิงลึก (Industries Transformation with Data Analytics and Consumer Insights)
โดยได้รับเกียรติจากวิทยากรพิเศษ ศักดิ์พัฒน์ วิทยศักดิ์ กรรมการผู้จัดการ บริษัท โซลดิฟ จำกัด ผู้เชี่ยวชาญด้าน การวางระบบคอมพิวเตอร์, อุตสาหกรรม 4.0 และระบบ IoT ในภาคอุตสาหกรรม
กรรมการกลุ่มอุตสาหกรรมดิจิทัล สภาอุตสาหกรรมฯ บรรยายในหัวข้อ “Industry Transformation Practice and Case” ขอสรุปประมวลความได้ดังต่อไปนี้
ศักดิ์พัฒน์ บรรยายว่า ในโลกของเทคโนโลยีในโรงงานอุตสาหกรรม แบ่งออกเป็น 2 ประเภทใหญ่คือ (1) เทคโนโลยีด้านการปฏิบัติการ (Operation Technology: OT) หมายถึง การใช้เทคโนโลยีเพื่อบริหารจัดการกระบวนการ และควบคุมเครื่องจักรในโรงงาน ให้สามารถดำเนินกิจกรรมได้ ตามความต้องการโดยให้เกิดการผลิตที่มีประสิทธิภาพ
และ (2) เทคโนโลยีสารสนเทศ (Information Technology: IT) หมายถึง การมีเป้าหมายในการควบคุมข้อมูล การจัดเก็บข้อมูล และการประมวลผลข้อมูล สามารถแยกย่อยออกเป็น การพัฒนาหรือจัดเก็บ และประมวลผลข้อมูล, การดูแลระบบให้สามารถทำงานได้, การช่วยเหลือผู้ใช้งานระบบให้สามารถทำงานได้ และดูแลโครงสร้างพื้นฐานทางด้านเทคโนโลยีสารสนเทศให้อยู่ในสภาพที่ทำงานได้ตามปกติ
การเปลี่ยนผ่านสู่ระบบดิจิทัล อุตสาหกรรม 4.0 และ IOT
การเปลี่ยนผ่านดังกล่าวเป็นการประยุกต์ใช้เทคโนโลยีด้านดิจิทัลให้เข้ากับกระบวนการทำงานจากแบบเมนวลให้เป็นกระบวนการที่ใช้เทคโนโลยีเพื่อเพิ่มคุณค่าสู่ลูกค้า สามารถแบ่งได้ 4 ประเภท คือ กระบวนการทางธุรกิจ (Business Process), ตัวแบบทางธุรกิจ (Business Model), โดเมนธุรกิจ (Business Domain), และองค์กร (Organization) เป็นที่มาของการปฏิวัติอุตสาหกรรมในยุค 4.0 (Industry 4.0) ซึ่งเกิดขึ้นครั้งแรกที่ประเทศเยอรมัน
หลักการของอุตสาหกรรม 4.0
อุตสาหกรรม 4.0 จะมีลักษณะที่สำคัญ 4 ข้อคือ คือ (1) การทำงานร่วมกัน (Interoperability) หมายถึง ความสามารถของเครื่องจักร อุปกรณ์ เซ็นเซอร์ และผู้คนในการเชื่อมต่อและสื่อสารระหว่างกันผ่านเทคโนโลยี Internet of Things (IoT) (2) ความโปร่งใสของข้อมูล (Information Transparency) หมายถึง ความสามารถของระบบสารสนเทศในการสร้างสำเนาเสมือนของโลกทางกายภาพโดยการเพิ่มแบบจำลองโรงงานดิจิทัลด้วยข้อมูลเซ็นเซอร์
(3) ความช่วยเหลือด้านเทคนิค (Technical Assistance) หมายถึง ความสามารถของระบบความช่วยเหลือเพื่อสนับสนุนมนุษย์โดยการรวบรวมและแสดงข้อมูลอย่างเข้าใจ ความสามารถของระบบกายภาพทางไซเบอร์ในการสนับสนุนทางกายภาพของมนุษย์ และ(4) การตัดสินใจแบบกระจายอำนาจ (Decentralized Decisions) หมายถึง ความสามารถของระบบกายภาพทางไซเบอร์ในการตัดสินใจด้วยตนเองและดำเนินงานของตนอย่างอิสระที่สุด
4 ขั้นตอนของอุตสาหกรรม 4.0
ประกอบไปด้วย (1) การเชื่อมต่อ (Connectivity) คือ แปลง Physical เป็น Digital การจัดเก็บข้อมูล การสร้างภาพกระบวนการ,การบูรณาการ ERP/MRP (2) ประสิทธิภาพ (Efficiency) คือ การเพิ่มประสิทธิภาพการผลิต, ประสิทธิภาพของอุปกรณ์โดยรวม การควบคุมคุณภาพ
(3) การวิเคราะห์ข้อมูล (Data Analytic) คือ การคาดการณ์การบำรุงรักษา, การวางแผนอย่างชาญฉลาด และ (4) วิวัฒนาการของตัวแบบทางธุรกิจ (Business Model Revolution) คือ ธุรกิจใหม่, ตัวแบบใหม่ และโดเมนใหม่
IOT ในโลกอุตสาหกรรม
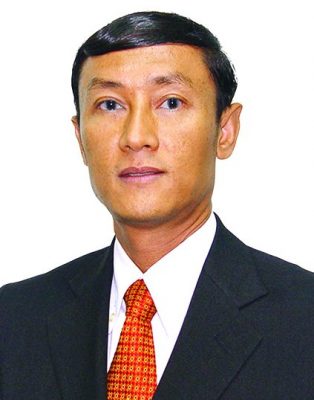
IoT หรือ อินเทอร์เน็ตของสรรพสิ่ง คือแนวคิดในการเปลี่ยนข้อมูลกายภาพให้เป็นดิจิทัล เพื่อสื่อสารบนเครือข่ายแบบอินเทอร์เน็ตได้ ดังนั้น_IoT ในอุตสาหกรรม (Industrial Internet of Things: IIoT) คือ การนำเทคโนโลยี IoT มาใช้ในการแปลงข้อมูลกายภาพภายในโรงงานทั้งจากเครื่องจักรสภาพแวดล้อม และมนุษย์เป็นข้อมูลดิจิทัลสื่อสารบนเครือข่ายแบบอินเทอร์เน็ต
อุปสรรคของ IoT_ในอุตสาหกรรม คือ ใช้อุปกรณ์ IoT ที่ไม่เหมาะสมกับสภาพแวดล้อม, ความปลอดภัย, มาตรฐาน, อายุการใช้งาน, เครื่องจักรที่เชื่อมต่อมีโอกาสจะถูกโจมตี เพราะว่าสามารถควบคุมเครื่องจักรทางไกลได้, การออกแบบที่ไม่ดีทำให้เกิด Network Overload และค่าใช้จ่ายที่ไม่จำเป็น เนื่องจากข้อมูลอาจมีการซ้ำซ้อนกันได้
การเปลี่ยนผ่านโรงงาน (TRANSFORM FACTORY)
คือ การทำการเปลี่ยนผ่านสู่ดิจิทัล ในโรงงานจะเป็นการบูรณาการเทคโนโลยีเข้ากับส่วนที่เป็นกายภาพและมีผลกระทบต่อกระบวนการผลิตค่อนข้างสูงทั้งในส่วนของนวัตกรรม, การปรับปรุงประสิทธิภาพการดำเนินงาน, การออกแบบผลิตภัณฑ์, การขนส่งและความสัมพันธ์กับลูกค้า
การทำ Digital Transformation จะเป็นการทำ IT OT Convergence เพื่อบูรณาการทุกอย่างเข้าด้วยกัน ในส่วนของ IT นั้นคือเป็นการบูรณาการส่วนที่เกี่ยวกับจัดเก็บข้อมูลและประมวลผลเข้ากับ OT ที่เป็นส่วนจัดการกระบวนการผลิต ความท้าทายของการเปลี่ยนผ่านโรงงาน
คือ ฝ่าย IT ต้องเพิ่มความรู้ความสามารถในการใช้เทคโนโลยี เพื่อบูรณาการ Hardware, Software, System, Security, ต้องมีการลงทุนเพิ่มในการใช้เทคโนโลยีเพื่อเชื่อมต่อเครื่องจักร, สภาพแวดล้อม และบุคลากร, ในโรงงานในเรื่องของงานดำเนินการตามตารางงานที่ไม่ยืดหยุ่นการหยุดกระบวนการ
อาจก่อให้เกิดต้นทุนค่าเสียโอกาสทำให้หลายโรงงานยังไม่สามารถปรับปรุงได้เต็มที่, งบประมาณที่จำกัดทำให้จัดหาระบบโดยใช้งบประมาณเป็นตัวผลักดันมากกว่าเป้าหมาย
การเปลี่ยนผ่านโรงงาน: พื้นที่ทำงาน (Transform Factory: Function Area) ได้แก่
(1) กระบวนการวิจัยและพัฒนา-การปรับปรุงกระบวนการ, การปรับปรุงสินค้า, การปรับปรุงประสิทธิภาพการผลิต (2) กระบวนการควบคุมการผลิต-การบริหารการผลิตรวมถึงการบริหารทรัพยากรต่างๆ ที่เกี่ยวข้องกับการผลิต (3) กระบวนการจัดการคุณภาพ-การควบคุมมาตรฐานการผลิตและมาตรฐานสินค้าและการปรับปรุงเพิ่มคุณภาพ
(4) กระบวนการบำรุงรักษา-การดูแลเครื่องจักรและสภาพแวดล้อมในโรงงาน (5) กระบวนการวางแผน-จัดการด้านการวางแผนโดยประสานงานกับฝ่ายผลิต
กรณีศึกษา: การเปลี่ยนผ่านกระบวนการผลิต
กรณีศึกษาที่ 1 ผลิตภัณฑ์ คือ ผ้าย้อมสำหรับอุตสาหกรรมรถยนต์, เป้าหมาย คือ ควบคุมการผลิตด้วยระบบ Barcode และดึงข้อมูลสินค้าและการตรวจสอบคุณภาพจาก Sensor, ความท้าทาย คือ มีการแทรก Order และเปลี่ยนแปลง Order, ผลลัพธ์ คือ การตรวจสอบย้อนกลับ และประสิทธิภาพในส่วนงาน QC
กรณีศึกษาที่ 2 การผลิตอุปกรณ์มือถือ (Mobile Production) ผลิตภัณฑ์ คือ อุปกรณ์แต่งรถ Cartoon สำหรับ Super Car, เป้าหมาย ใช้ Mobile Computer ในการควบคุมการผลิต, ความท้าทาย คือ การผลิตด้วยมือ, ผลลัพธ์ คือ การจัดการกระบวนการผลิตแบบเรียลไทม์
กรณีศึกษาที่ 3 การจำลองเสมือนจริงของเครื่องจักร (Machine Virtualization) ผลิตภัณฑ์ คือ ขวดและภาชนะเก็บความร้อนและความเย็น, เป้าหมายคือ Visualize Machine ด้วย SCADA และเก็บข้อมูลจาก PLC เพื่อวิเคราะห์ Defect, ความท้าทาย คือ PLC ไม่รองรับ, ผลลัพธ์ คือ ใช้ข้อมูลประวัติ เพื่อทำการวิเคราะห์